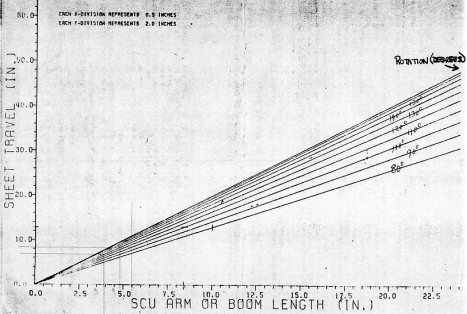
Harris Engineering of Springfield, Va. has furnished the following excellent article, WINCHRAFT #1: which we reprint here with the permission of Bob Harris. (1979)
"You say you're having trouble figuring out how to set up your HERCULES or Little Herc? -- or somebody else's swingarm Sail Control Unit? Perhaps the following thoughts will help.
1. Think of the moving arm of the winch as forming 2 sides of an isosceles
triangle when it is full in and full out -- or if you like it better, at one end of its travel and the other. You can measure it better, at one end of its travel and the other. You can measure the included angle between the two equal sides formed by the two positions of the winch arm -- right? Now, the third side (the hypotenuse for you geometricians) is the distance the sheet line will travel, if it is tied to the end of the arm, and the winch is operated through its full travel. So, the question really is, how do you find the hypotenuse of an isosceles triangle? Well, the formula:
a = 2c sin A/2
Where a is the hypotenuse, c is the length of the SCU arm from pivot to the point of sheet attachment, and A is the angle included between the two end positions of the SCU arm. It also happens that the included angle is 90 degrees (a right angle) the hypotenuse length is 1.414 times the effective length of the SCU arm.
This then will tell you how much sheet travel you can get from a swinging arm SCU Obviously it depends on how long the arm is, and where the limit switches stop the unit from further rotation.
2. Next problem is, how much sheet line travel do you need? Well, if you think about it a moment, the same isosceles triangle setup applies, for example, to your main boom. The length of "c" in the formula above is the distance from your boo,.-.1 gooseneck swivel to the place the sheet line attaches to the boom, and the angle A is the angle from the centerline of the yacht to the place where your boom hits the sidestay - OK? Looking at the formula again, then, "a" has to be the hypotenuse,or the length of the sheet line needed to let the boom move from midships to full out. Again, obviously, how much sheet line you need depends on how far out on the boom the sheet line is attached, and how far you want the boom to swing. If it happens to be 90 degrees, you need 1.414 times the length of the boom for swivel to sheet attachment point.
3. Next question is, where's your high school trig book -- the one with the sine table in it? Your wife threw it out with your WW2 uniform. Never fear! Harris_ has thought of everything. Take a look at the attached graph(separate post). Let's assume you are working on a. kit yacht whose manufacturer has told you where to bring the sheet out through the deck (and, I hope) to attach it to the boom directly above the exiting point.
--
First, find the effective length of the boom. Let's assume it is 10 inches, and that inspection of the drawings tells us that 80 degrees of boom swing is needed.
Enter the graph on the horizontal axis (SCU- arm or boom length) at the 10" mark and go directly up until the 10" line intersects the 80 degree diagonal line.
--
Now go horizontally from that point to the left and you will read, the vertical axis, less than 13 inches (which is the amount of sheet travel you need.
--
Now how to make the SCU give it to you?
Well, let's again assume that .at your SCU is set right now for 100 degrees of travel between limits. So, come back from the left side at the 13 inch point, until you intersect the 100 degree diagonal and then drop straight down.
You'll find that you hit the horizontal axis at just short of 8 1/2". This is the length arm needed on your SCU.
4. What's that? It won’t fit the hull. The arm is too long? Great Ceasar's Goat:! Seriously, don't panic all will be well. Using our winch-craft, lets's cast a spell, and fix, the problem.
The graph we're working with is built on the assumption that the sheet end is attached to the winch arm, (what us experts call "single purchase" and all we have to do is pass the sheet line through the SCU arm hole to which the sheet line was to be tied, and run it back in the direction it
came from, securing it to something, in the hull.
I like to use a small wood block with a screweye in it. Now, when the arm moves, it will -move twice as line for the same amount of rotation, so we can use an arm exactly half as long—or 4 1/2 inches. 1f that won' t fit in your yacht, it' is a submarine and you have been. misled! Actually, you can go as far as triple purchase arrangements this way, but I don't recommend going further than that.
5. Don't worry about being too, too precise in all this. -First the line you us stretch a bit, anyway, you’ll make your touch-up adjustments in boat, if you’re smart.